What is Hardware-in-the-Loop (HIL) Testing?
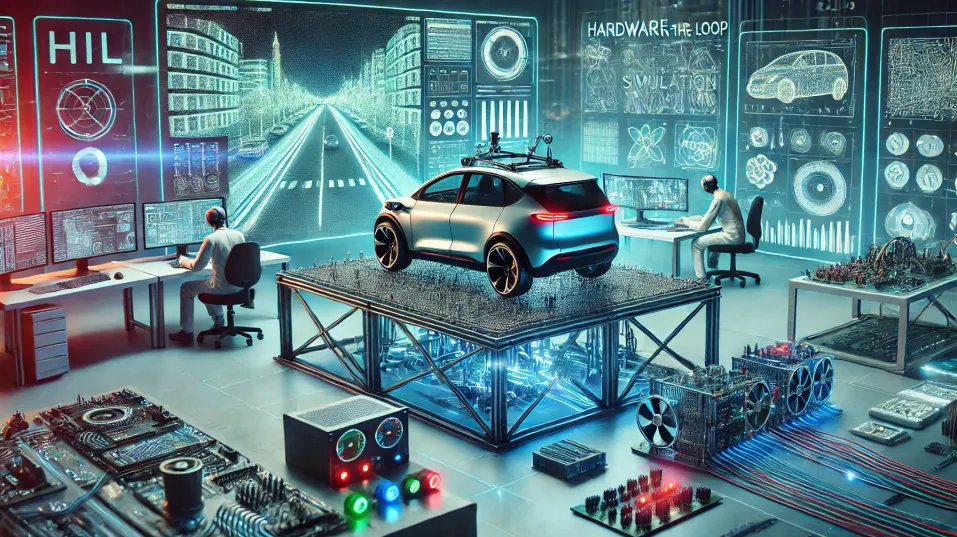
Hardware-in-the-loop (HIL) Testing is a simulation-based method for testing and validating real-time embedded systems. By connecting a controller to a test system that emulates real-world conditions, HIL allows thorough evaluation without needing physical prototypes. This approach reduces costs, minimizes risks, and ensures reliable performance before actual deployment.
How Hardware-in-the-Loop Testing Works?
HIL testing combines real hardware with simulated environments to validate system performance before real-world deployment. It ensures seamless interaction between control units, sensors, & software under controlled conditions.
Here's how it works in an automotive setup:
- Simulation Setup: HIL testing utilises real-time simulation models that replicate the following:
- Vehicle dynamics: Acceleration, braking, suspension behaviour.
- Environmental conditions: Road surfaces, weather impacts, traffic scenarios.
- Controller Interaction: Under test, the Electronic Control Unit (ECU) receives simulated sensor data (e.g., radar, LiDAR, GPS, cameras). The ECU processes these inputs and makes control decisions like an actual vehicle.
- Feedback Loop: The simulated environment provides continuous feedback based on ECU outputs.
Engineers analyse system behaviour and make necessary adjustments before physical implementation.
Why is HIL Testing Important?
Hardware in the loop (HIL) testing is essential for developing and validating embedded systems because it can simulate real-world conditions and uncover potential issues before physical prototypes are created.
Below are key reasons why HIL testing is essential:-
- Early Issue Detection: Identifies software and hardware integration problems early in the design process, reducing costly errors.
- Cost and Time Efficiency: This method minimises development costs and time by allowing rapid testing of numerous scenarios without physical prototypes.
- Enhanced Safety: Simulates dangerous scenarios safely, which is crucial for industries like automotive and aerospace, where safety is critical.
- Comprehensive Test Coverage: Provides thorough validation across various operating conditions and edge cases through automated testing.
- Improved Product Quality: This ensures the reliable performance of control units, sensors, and software, leading to higher-quality products.
- Support for Complex Systems: Effectively evaluates advanced technologies like ADAS and IoT devices in real-time environments.
- Risk Mitigation: Essential for critical applications to ensure safety and compliance with regulatory standards, reducing the likelihood of failures.
HIL testing is vital for accelerating innovation while ensuring reliability and safety in complex embedded systems
Key Components of Hardware-in-the-Loop Testing
Device Under Test (DUT)
- ECUs for ADAS, powertrains, braking systems, infotainment, and battery management.
Real-Time Simulation Platform
- Runs models of vehicle behavior, sensor fusion, and environmental factors.
- Examples include dSPACE, NI VeriStand, Speedgoat, and Typhoon HIL.
I/O Interfaces
- Communication buses: CAN, LIN, FlexRay, Ethernet.
- Sensor signal emulation: Analog, digital, PWM signals.
- Actuator emulation: H-bridges for motor controllers, resistive loads for battery systems.
Benefits of HIL
HIL testing offers significant advantages by enhancing system validation efficiency, safety, & accuracy. It reduces costs, improves test reliability, and enables the simulation of critical scenarios without real-world risks. Here are the key benefits:
Cost Efficiency
- Reduces dependency on physical prototypes and extensive road testing.
- Detects software issues early, minimising expensive hardware failures.
Safety
- Enables testing of hazardous scenarios (e.g., brake failure, battery overheating) in a virtual setup.
- Prevents risks associated with high-voltage testing in EVs.
Repeatability
- Provides consistent test conditions, eliminating variability found in road testing.
- Facilitates automated testing for regulatory certification.
Speed & Scalability
- Speeds up development cycles through parallel testing.
- Supports scalable configurations for different vehicle models and architectures.
HIL Simulation with MATLAB and Simulink
Hardware-in-the-Loop (HIL) simulation is a way to test and validate control systems in real-time by combining simulated systems with actual hardware. It bridges the gap between purely simulated models and physical prototypes so you can test software and hardware interaction in realistic conditions. MATLAB and Simulink is a great platform for HIL because of the comprehensive tools for modeling, simulation, real-time code generation and hardware interfacing.
In HIL simulation the system is divided in two parts: the plant model (a simulated representation of the physical system) and the controller (running on actual hardware or a real-time target). Simulink is used to design and simulate the plant and control algorithms, and MATLAB for analysis and visualization.
The process involves:
- Model Development: Create a high-fidelity model of the plant in Simulink, possibly using Simscape for physical systems.
- Controller Design: Design and validate the control algorithm in MATLAB/Simulink.
- Code Generation: Use Simulink Coder to generate real-time code for the hardware.
- Hardware Integration: Connect the hardware (e.g., Speedgoat, dSPACE) to the simulation through real-time I/O interfaces.
- Testing and Validation: Simulate, analyze and refine.
HIL simulation with MATLAB and Simulink is a cost-effective, risk-mitigated way to design verification, no need for full-scale prototypes and test edge cases before deployment.
Future of Automotive Safety
With the rise of autonomous vehicle technology, HIL systems are becoming even more critical. They provide a flexible way to test new technologies and ensure that all the components of a vehicle work together safely. This is especially important for features like ADAS, where real-world testing could be risky.
Hardware-in-the-loop testing allows engineers to fine-tune performance in a safe, virtual environment for features like lane-keeping, adaptive cruise control, and emergency braking, helping to move closer to safer and smarter roads.